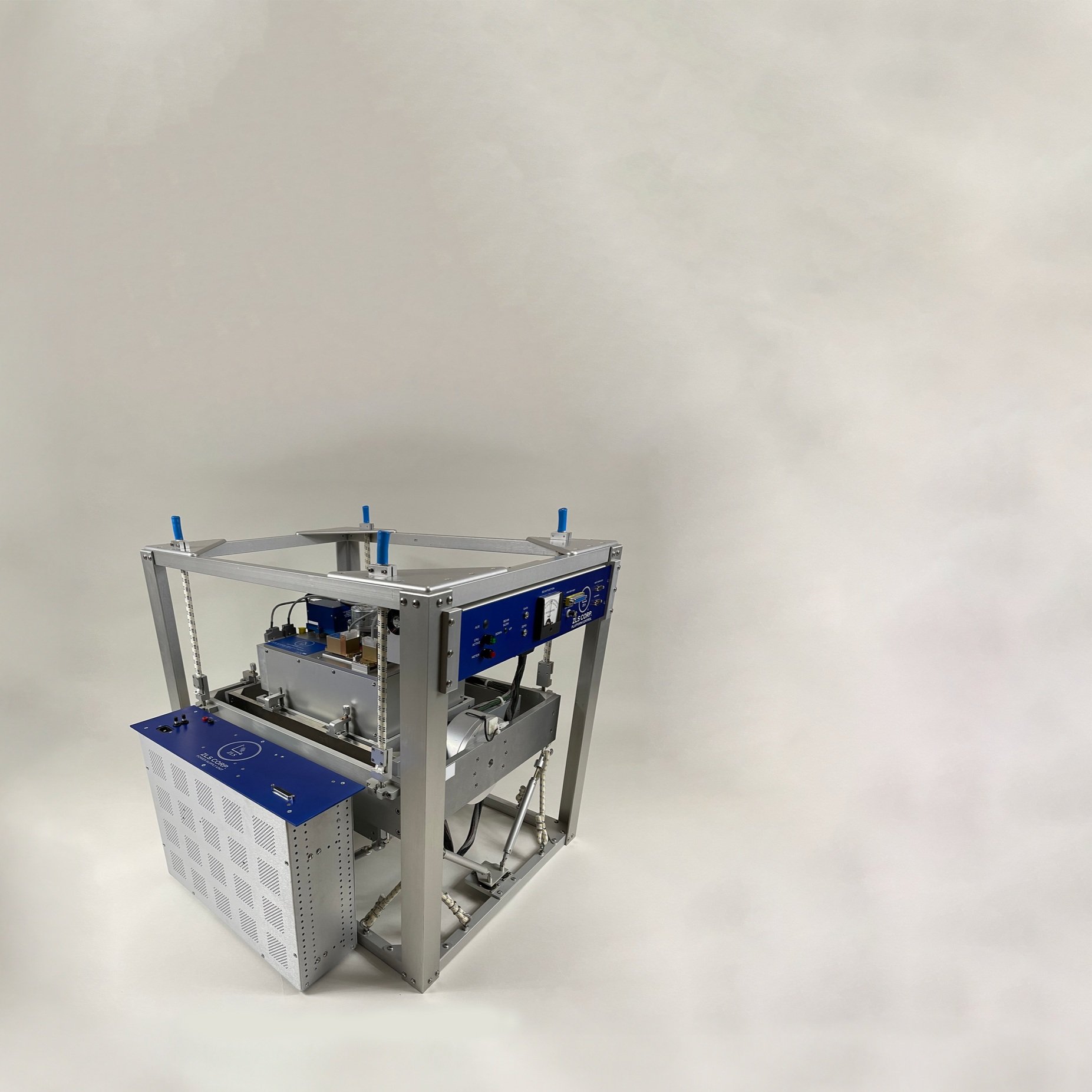
The ZLS Dynamic Meter with UltraSys Control System
Introduction
After nearly three years of research and development ZLS has introduced a meter for marine applications. The ZLS Dynamic Meter is a completely new meter designed to eliminate inherent cross-coupling errors, frequent damper adjustments, and vibration sensitivity problems associated with beam-type gravity meters.
Features of the Dynamic Meter
The new sensor eliminates the cross-coupling errors inherent in older beam-type gravity meters by constraining the proof mass to vertical linear motion.
Damper adjustments are no longer required.
The new sensor utilizes liquid damping that virtually eliminates the sensitivity to vibration common in air-damped sensors.
Residual imperfection errors, due to minute variations in manufacture of the system are typically three to five times smaller than those for beam type sensors. Unlike beam type meters, imperfection errors are stable with time and do not require regular testing to track changes.
The new design eliminates the “slope error” prevalent in beam meters that causes reading errors with beam position under dynamic conditions.
Improved Accuracy and Enhanced Reliability
Damper Adjustments no longer required.
Eliminates the cross-coupling errors inherent in older beam-type gravity meters.
Residual imperfection errors are typically three to five times smaller than beam meters.
Liquid damping virtually eliminates the sensitivity to vibration common in air-damped sensors.
Eliminates the “slope error” prevalent in beam meters.
The system utilizes the field proven ZLS FogPack.
The system utilizes the ZLS UltraSys control system that is the standard of the industry. ZLS has upgraded approximately 75% of currently operating Model S gravity meters with its control systems.
Features of the UltraSys Control System
Digital techniques replace analog hardware, eliminating electronic drift and enhancing system reliability.
Fully automatic system will start and function unattended after a power interruption.
Full manual control through menu selection.
200 Hz data sample rate accurately digitizes sensor, gyro and accelerometer signals assuring no loss of signal information.
200 Hz update of platform feedback loops provides superior platform control.
Simultaneous data output to video monitor, hard disk, serial port, and printer.
Graphic or digital format may be selected for printer output.
Alarm function shuts down system and provides a remote alarm signal in the event of a serious system malfunction.
Keyboard log records all keyboard activity for review.
Complete testing and final adjustment using the ZLS test facility.
Self-contained precision gyro power supply and servo amplifiers.
Two-year limited warranty.
How UltraSys Functions
UltraSys utilizes an embedded processor to perform all of the platform and sensor control functions. The power module may be located anywhere within three (3) meters of the platform. A host computer, connected to the control module with a serial cable, completes the system.
The embedded processor is connected to a host computer through a serial port. Using ZLS-supplied software, the host computer processes the data as required for high resolution or standard marine operations and archives the final data.
Raw data from the accelerometers, gyros, and gravity transducer are digitized 200 times a second with a 16-bit A/D converter and processed by the embedded computer. Analog signal outputs to control the motor and gyros are provided by a 16-bit D/A converter, which is also updated at 200 Hz. Slightly filtered data are transmitted to the host computer once per second.
The host computer stores all data on hard disk and can simultaneously direct data to the video monitor, serial port, and printer in a variety of formats. Either a numerical or graphical format may be selected for display on the printer. In high-resolution marine and airplane modes, raw data are recorded once per second, allowing the user to custom filter the data for specific applications. In marine mode the data are filtered in appropriate manner for marine data and recorded at 10-second intervals.
Additional external data may be appended to the gravity data. The system accommodates up to four analog channels and a 24-bit digital channel. The system is fully automatic and will start unattended after a power interruption. Operation is as simple as turning on the switch. However, all system functions can be controlled manually through menu selections. All keystrokes are logged in a separate file for a complete record of system activity. System functions are continuously monitored and UltraSys will automatically shut down and activate an external alarm signal in the event of a serious malfunction.
UltraSys is Fully Digital
Transducer outputs are digitized with little additional analog processing. The ZLS system digitizes input signals 200 times a second. All processing, including filtering, is done digitally. All control-loop algorithms, for both the platform and gravity sensor, are performed digitally by an embedded computer. Eliminating analog circuits enhances reliability and simplifies servicing.
A Mature System
Herbert D. Valliant, co-founder of ZLS Corporation, developed the prototype at the Geological Survey of Canada (Geophysics, 50, 840-845, 1985.)
Accuracy of the Operating System
The accuracy of a marine gravity meter is difficult to specify as it is dependent on the characteristics of the ship, the sea-state, and accuracy of navigation (typically 1mGal).
ZLS’s full digital control system enhances overall system accuracy by eliminating the gain and offset drifts that are inherent with analog electronics. It permits the platform and sensor control parameters to be set more precisely. In analog systems, these parameters are adjusted by changing electronic components, whereas, in digital systems, they are adjusted by simply entering a number in the computer.
Specifications
Sensor
Type: Metal Zero-Length Spring hardened metal micrometer screw
Range: Worldwide 7,000 mGal marine
Temperature range: -15 to +50° C
Drift: 3 mGals or less per month after aging
Static Repeatability: <0.1 mGal
Stabilized Platform
Pitch: +/- 25 degrees
Roll: +/- 30 degrees
Period: standard 4 minute, optional 16 minute
Damping: 0.707 of critical
Control System
Power Requirements: 87 to 270 VAC 47 to 63 Hz single phase
Power Consumption: Operation: 1 Amp*, Maximum: 2.5 Amp* *measured at 117 Volts @ 60 Hz.
Resolution of Recorded Data: 0.01 mGal
Clock and Gyro Power Source: Frequency: 200Hz
Temperature stability: 5 ppm -20°C < T < +70°C
Short term aging: 1 X 10^-9/sec
Adjustability: Sufficient for 5 years of aging.
External Outputs
Digital: 24 bit TTL compatible input
Analog: 4 channels, 16 bit resolution, gains of 1, 2, 4, or 8 may be selected by menu
Sample rate 200 Hz
Deliverables
ZLS Dynamic Sensor
ZLS Stabilized Platform
System Control Module: attaches to the platform frame
Universal Worldwide Power Supply: freestanding
Host Software: processes data for high resolution or standard marine operations
Comprehensive User’s Manual
Limited two-year warranty
Dimensions
Stabilized Platform and Sensor: 27 in wide; 22 in deep; 25 in high (70 cm wide; 55 cm deep; 64 cm high)
System Control Module: 19 in. wide; 5.5 in. deep; 3.5 in. high (48 cm. wide; 14 cm. deep; 9 cm. high)
Power Supply Module (Desktop Package): 21 in. wide; 18 in. deep; 7 in. high (53 cm. wide; 46 cm. deep; 18 cm. high)
Weight
Stabilized Platform and Sensor: 185 lb. +/- 5 lb. (83.9 kg. +/- 2.3 kg.)
System Control Module: 6 lb. (2.7 kg.)
Power Supply Module (Desktop Package): 36 lb. (16 kg.)
Specifications are subject to change without notice. Results may vary depending on conditions.